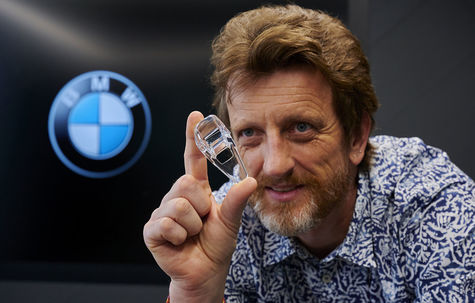
Mașini produse prin imprimare 3D? Tehnologia e încă în dezvoltare, dar BMW face pași masivi în această direcție
Fiecare dintre piesele care compun o mașină trebuie produsă cu ajutorul unei matrițe. Iar când 10.000 de piese înseamnă 10.000 de matrițe, costurile și timpul de producție cresc simțitor. Tehnologia imprimării 3D de componente din plastic și metal promite să rezolve această problemă. Și să facă piesele mai rezistente și mai ușoare.
Atunci când BMW a prezentat SUV-ul X7, acum doi ani, grila supradimensionată față de ceea ce oferea marca germană în gamă a atras atenția întregii lumi. De la meme și glume la discuții aprinse pe forumurile dedicate mărcii, pasionații auto au disecat toate implicațiile unei mutări din partea departamentului de design BMW. Mutare care, urma să observăm pe modelele lansate și prezentate ulterior, urma să devină unul dintre reperele estetice ale noii generații de modele ale brandului bavarez.
Seria 7, Seria 4 și, cel mai recent, SUV-ul full-electric iX sunt reprezentanții cei mai cunoscuți ai trendului grilei masive. Însă ce se spune foarte puțin este că în spatele acestei grile masive stă o poveste tehnologică care nu are legătură cu designul decât din perspectivă practică. Și în care BMW a investit zeci de milioane de euro în ultimii 30 de ani din postura de pionier al tehnologiei.
SECRETELE UNEI GRILE IMPRIMATE 3D
Este vorba de procedeele de imprimare 3D, pe care BMW le privește ca pe unul dintre factorii-cheie ai industrializării sub forma "toolless production", așa cum este denumită producția de componente standard fără utilizarea matrițelor clasice, ci prin imprimarea pieselor și componentelor din plastic și metal la imprimante industriale 3D.
Procesul este cunoscut în lumea ingineriei sub denumirea de producție aditivă, explicația termenului fiind aceea că piesele sunt produse prin turnarea de straturi peste straturi cu ajutorul unei imprimante hi-tech care funcționează așa cum îi dictează un software dedicat.
Pe scurt, atunci când trebuie produsă în serie fiecare dintre cele peste 10.000 de piese din care este formată o mașină modernă (de la componente ale motorului la piese de caroserie), primul pas al acestui proces este dezvoltarea de matrițe pentru fiecare dintre acestea. Tehnologia de imprimare 3D a pieselor face ca banii necesari acestui pas să fie economisiți, iar timpul în care o mașină este transformată din concept în model de serie să se scurteze serios.
În cazul lui iX, grila frontală imensă nu este doar un element constructiv al mașinii, așa cum se întâmpla până acum, ci un subansamblu complex care în spatele său integrează o armată de senzori și de conectori electronici ce trebuie așezați într-o structură geometrică extrem de complexă imposibil de produs cu ajutorul unei matrițe clasice. Altfel spus, grila regândită a modelelor BMW reprezintă o demonstrație de redefinire a funcționalității unui element tradițional. Dacă grila avea până acum rol estetic și de aerisire a componentelor radiatorului, ultimii ani dezvoltând chiar și o componentă aerodinamică, aceasta devine de acum un simbol al modificărilor majore prin care trece industria auto la nivel tehnologic.
Dezvoltată la Centrul Tehnologic de Materiale Ușoare și Tehnologie din Landshut, la nord-est de Munchen, grila lui BMW iX este direct derivată din cea a conceptului iNext și devine o componentă multifuncțională și inovatoare care-și păstrează componenta estetică, dar plusează cu un aport tehnologic masiv, fiind "centrul de comandă" al unei armate de sisteme de siguranță activă și de automatizare a rulării.
UN CAMPUS DEDICAT IMPRIMĂRII 3D
Pentru a putea genera economii la scară industrială prin tehnologia de imprimare 3D și pentru a introduce acest procedeu ca parte componentă în producția de serie, cei de la BMW au deschis recent ceea ce constructorul bavarez numește un Campus de Producție Aditivă la Oberschleissheim, o localitate aflată în apropierea orașului München. BMW a investit 30 de milioane de euro în acest sit de producție atipică, unul dintre rezultatele vizibile ale unei implicări tehnologice care în cazul bavarezilor durează deja de trei decenii.
Cu ajutorul a 80 de angajați dedicați și a 50 de imprimante 3D industriale de dimensiuni apreciabile, centrul de la Oberschleissheim este capabil să producă piese și subansamble de diferite dimensiuni atât pentru conceptele pe care le pregătește BMW, cât și pentru mașinile de serie viitoare sau din istoria companiei. Asta pentru că, de exemplu, un mâner rotativ din metal care coboară geamurile laterale ale unui BMW 507 este mult mai ușor , mai rapid și mai ieftin de produs astfel decât cu ajutorul unei matrițe dedicate.
Cei de la BMW susțin că BMW a produs astfel peste un milion de piese în ultimii 10 ani, iar în 2019 au ieșit "din imprimantă" 300.000 de piese utilizate în diverse variante pe produsele sau viitoarele produse concepute de marca germană.
Pe lângă timpul de producție și costurile reduse, un alt avantaj foarte important al imprimării 3D este reprezentat de durabilitatea pieselor. Pentru că tehnologia a evoluat masiv în anii digitalizării, piesele produse astfel sunt în general mai rezistente și mai ușoare decât versiunile lor "tradiționale".
"La nivel de flexibilitate, tehnologia imprimării 3D e incomparabilă cu cea a producției de matrițe. Când inginerii au nevoie de o componentă nouă, informațiile sunt transmise digital dinspre departamentul de dezvoltare spre imprimanta 3D și procesate sub formă de piesă. Dacă respectiva piesă nu se ridică la nivelul cerut de ingineri în teste, ea poate fi modificată ușor pe computer și reimprimată imediat", explică inginerii BMW.
Unul dintre modelele care beneficiază deja de componente produse 3D este noul Rolls-Royce Ghost. Piesele printate 3D sunt asamblate la fabrica de la Goodwood și pot fi localizate atât "sub radar", adică în zonele invizibile ale mașinii, cât și în habitaclu. Conform inginerilor Rolls-Royce, acestea "oferă un nivel foarte înalt de funcționalitate și rigiditate"
Pe lângă producția pieselor, tehnologia poate să ajute chiar și la personalizarea mașinilor comandate de clienți. MINI oferă, de exemplu, semnalizatoare laterale cu numele proprietarului printat 3D pe un element din plastic. Opțiunea costă 150 de euro.
Scopul celor de la BMW este de a dezvolta această tehnologie înspre producția integrală de concepte, apoi de mașini de serie. Deocamdată, limitările de dimensiuni (o imprimantă de acest tip poate să producă piese de maximum 42x42x40 de centimetri) și cele legate de complexitatea materialelor păstrează încă o componentă experimentală în construcția 3D de piese și subansamble. Însă imprimantele care aplică straturi fine de pudră metalică sau de plastic și rășină lichidă care sunt lipite cu ajutorul laserului, razelor infraroșii sau ultraviolete reprezintă una dintre promisiunile tehnologice ale viitorului mașinilor.
Czinger 21C: deja prezentat, hybrid ( V8 twin turbo + 2 electrice ) . bmw poate e primul din cei mari care face asta, dar cei mici deja sant acolo.