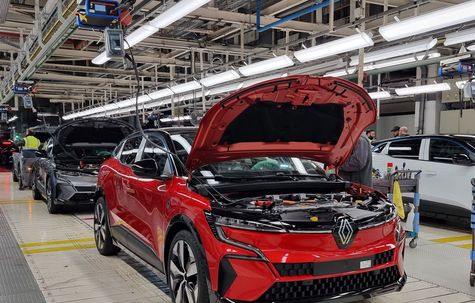
REPORTAJ: Am vizitat locul de naștere al lui Megane Electric, uzina Renault din Douai
La invitația celor de la Renault, am zburat la Paris și am vizitat uzina din Douai, aflată la circa 200 de kilometri de capitala Franței. Parte a complexului Renault ElectriCity, această uzină produce (printre altele) modelul Megane E-Tech Electric.
În urmă cu doi ani, șeful Renault, Luca de Meo, anunța crearea unui complex industrial, axat pe electrificare, care urma să cuprindă 3 uzine situate în nordul Franței. Totul se întâmpla în cadrul prezentării planului Renaulution.
Complexul, denumit Renault ElectriCity, integrează uzinele din Douai, Maubeuge și Ruitz, și intenționează să producă 400.000 de vehicule electrice anual, până în 2025.
La Ruitz se produc cutii de viteze automate, dedicate modelelor E-Tech (electrificate) din portofoliul Renault: Clio, Captur, Megane Estate și Arkana. În tot acest timp, uzina din Maubeuge asamblează modelul Kangoo și toate derivatele sale utilitare.
Tot la Maubeuge, Renault produce vehicule utilitare pentru nemții de la Daimler (Mercedes-Benz Citan) și Nissan (NV250).
La invitația celor de la Renault, noi am zburat la Paris pentru a vizita, poate, cea mai importantă uzină din complexul ElectriCity: cea de la Douai, situată la aproximativ 200 de kilometri de capitala Franței. Haideți să vă povestim ce se fabrică aici. Iar înainte de asta avem și un clip video cu anumite părți din procesul de asamblare, cum ar fi reunirea șasiului cu caroseria, montarea panourilor de caroserie și sudarea lor, precum și construirea pachetului de baterii.
AȘA SE ASAMBLEAZĂ RENAULT MEGANE ELECTRIC
GIGA UZINĂ DE BATERII, LA 100 DE METRI DE FABRICĂ
Spunem asta pentru că, la circa 100 de metri de fabrică, producătorul din Hexagon construiește o giga uzină de baterii Li-ion. Ea va avea o capacitate de producție de 9 GWh în 2024 și 24 GWh în 2030. Deci cuvântul „Giga” e pe deplin meritat.
Uzina Renault din Douai a fost înființată în 1970 și, de-a lungul anilor, a produs modele ca Renault 5, Renault 14, Renault 9/11, Renault Fuego, Renault 21, Renault 19, Talisman, Scenic și Espace.
Din 2022, în urma unor investiții de câteva zeci de milioane de euro, uzina din Douai a fost transformată pentru a putea produce modele electrice, dezvoltate pe arhitectura CMF-EV. Ne referim aici la Megane E-Tech Electric.
Așadar, în prezent, la Douai, Renault produce modelele Scenic, Espace și Megane Electric. În câteva zile, însă, producția lui Scenic și Espace va fi mutată, astfel că uzina se va concentra 100% pe producția de modele cu zero emisii.
NOI MODELE ELECTRICE VOR FI ASAMBLATE LA DOUAI
Alături de Megane Electric vor veni, în curând, Scenic electric și, din 2024, noul Renault 5 electric. Toate vor fi, așadar, produse în Franța, acesta fiind unul dintre lucrurile cu care se mândrește Renault ElectriCity.
"Chiar dacă ești economist sau jurnalist, începi să te întrebi dacă este posibil să construiești mașini în Franța. Deci, da, este posibil să produci mașini în Franța," susține Luciano Biondo, directorul Renault ElectriCity, în cadrul unui interviu pe care ni l-a acordat, cu ocazia vizitei.
Acesta recunoaște că producția unui automobil s-a schimbat în ultimii 10 - 20 de ani, dar că Renault "va reuși să producă în Franța o mașină profitabilă, prin schimbarea ecosistemului. Intenționăm să avem, pe o rază de maxim 200 de kilometri, toate componentele mașinii. [...] Spre exemplu, cutia bateriei (care acum este produsă în Serbia) pentru noua mașină o vom produce la 20 de kilometri de aici (n.r Douai)."
Uzina din Douai se întinde pe o suprafață de 118 hectare și cuprinde 32 de clădiri. Noi nu le-am putut vizita pe toate, dar în timpul avut la dispoziție am acoperit departamentele de Caroserie/Tinichigerie, Baterii și Montare/Asamblare.
LOCUL UNDE IA NAȘTERE SCHELETUL LUI MEGANE
Departamentul Caroserie/Tinichigerie cuprinde 3 clădiri și, momentan, produce "scheletele" pentru Scenic, Espace și Megane Electric. De la finalul acestei săptămâni, cei 300 de operatori care lucrează aici se vor ocupa numai de Megane Electric, producția celorlalte două modele urmând să fie mutată, după cum ziceam și mai sus. În cadrul vizitei am aflat că roboții care în prezent sunt folosiți pentru modelul Scenic vor fi vânduți sau vor fi trimiși la alte uzine, unde vor asambla alte produse.
Pentru Megane E-Tech Electric a fost gândit un proces nou de asamblare: producția este automatizată în proporție de peste 90%. În plus, toți roboții sunt conectați între ei pentru a putea urmări întregul proces de producție în timp real.
Fiecare platformă are o greutate maximă de 700 de kilograme (inclusiv portierele din aluminiu). Atunci când oamenii și roboții lucrează în perfectă armonie, o platformă este finalizată în 2.5 ore. Așa se face că Departamentul de Caroserie/Tinichigerie are o capacitate de producție de 35 de vehicule pe oră.
În viitorul nu foarte îndepărtat, aici vor fi instalați roboți suplimentari, astfel că această capacitate va ajunge la 60 de vehicule pe oră.
După ce sudează fiecare componentă a platformei, tot roboții sunt cei însărcinați cu verificarea lor din punct de vedere al calității. 4 roboți măsoară 131 de caracteristici în timp real. O operațiune care crește nivelul de calitate și eficientizează procesul.
Departamentul încorporează și o secție de Mentenanță, care se ocupă, printre altele, cu monitorizarea procesului de fabricație. În plus, cei care lucrează aici analizează acest proces și caută încontinuu soluții pentru a-l eficientiza.
AM VĂZUT CUM SUNT ASAMBLATE BATERIILE LUI MEGANE ELECTRIC
După ce am văzut cum ia ființă scheletul unui Renault Scenic, Espace și Megane Electric, următoarea oprire a fost la atelierul care se ocupă cu fabricarea bateriilor pentru acesta din urmă.
Ulterior, aici vor fi asamblate și bateriile pentru Scenic electric și R5 electric.
Departamentul lucra anterior la nașterea modelelor termice, astfel că a fost nevoit să treacă printr-o transformare și să se adapteze noii tendințe. Toată această schimbare a făcut ca, pe lângă operațiunile manuale, să își facă loc mai mult procese automatizate. De menționat că în acest atelier lucrează în jur de 30 de persoane.
Fiecare baterie este asamblată pe un cărucior special și are la bază un kit gândit chiar de Renault. Sunt fabricate aici 4 tipuri de baterii, cu capacități de 40 și 60 kW.
Acumulatorul de 40 kW are 8 module, iar cel de 60 kW este compus din 12 module, așezate cu grijă de roboți.
Ca o curiozitate, atelierul are, în prezent, o capacitate de producție de 30 de baterii pe oră. De anul viitor, odată cu intrarea lui Renault 5 electric în producție, capacitatea va crește la 60 de baterii pe oră.
După ce am urmărit cum roboții așează meticulos fiecare componentă a bateriei, am aflat că fiecare acumulator este mai apoi verificat. Un proces în care sunt implicați și oamenii. Numai după această inspecție, bateria este închisă și declarată conformă.
Urmează apoi două teste de etanșeitate. Pentru că bateria va fi montată sub vehicul, fiind expusă la factori externi, este testat circuitul de răcire și mai apoi etanșeitatea la aer și apă.
BATERIILE TREC PRINTR-O SERIE DE TESTE
Nici acum procesul de fabricație nu este complet. După toate acestea, bateriile sunt duse într-o încăpere specială unde va fi realizat testul de încărcare.
Potrivit legislației în domeniu, fiecare acumulator de 60 kW este încărcat la 37%. Un ciclu de încărcare durează 20 de minute și este împărțit în felul următor: 10 minute sunt dedicate diverselor teste, iar 10 minute pentru încărcarea efectivă.
În prezent, atelierul de baterii de la Douai integrează 12 stații de încărcare, dar numărul lor va crește la 14, odată cu venirea lui Scenic electric.
Abia după toate aceste teste, o baterie este completă și este gata să se întâlnească cu scheletul unui Megane Electric.
DEPARTAMENTUL DE MONTARE/ASAMBLARE
Ultimul departament pe care l-am vizitat a fost cel de Montare/Asamblare. Un loc unde, din nou, oamenii lucrează cot la cot cu roboții pentru ca un conglomerat de metal și cabluri să devină o mașină perfect funcțională.
Secția de montare are peste 75.000 de metri pătrați. Aici lucrează 1.100 de oameni pe 500 de posturi. Integrează 1.2 kilometri de linie de fabricație, iar aici sunt produse 500 de vehicule în fiecare zi.
Așa cum spuneam, momentan sunt asamblate aici 3 modele, dar 2/3 din producție este reprezentată de Megane E-Tech Electric. Până la urmă, cele peste 50.000 de comenzi, înregistrate de anul trecut și până acum, trebuie onorate.
Aprovizionarea liniilor de asamblare se face cu ajutorul unor roboți automați, cu ghidaj, care transportă cărucioarele cu piese pe trasee pre-stabilite. Aceștia sunt denumiți AGV și este foarte interesant de văzut cum își croiesc drum printr-un mini furnicar plin cu oameni și mașinării.
Secția este împărțită în 4 zone de "kitting", adică oamenii stau la postul de lucru, iar piesele care urmează să fie instalate le sunt aduse de acești roboți AGV.
Dacă tot suntem la acest capitol, mai trebuie spus că, la uzina din Douai, Renault practică o așa numită aprovizionare cu piese sincronizată. Pe scurt, furnizorul de piese este în apropierea uzinei și, mulțumită unui flux real de informații, știe (cu 2-3 ore înainte) ce piese sunt necesare.
Departamentul de Montare/Asamblare este locul unde platforma se unește, într-un final, cu caroseria. Nu înainte, însă, de o nouă verificare în ceea ce privește calitatea. Prima instalată este garnitura din spatele mașinii, iar planșa de bord este adusă pe o linie secundară.
Pentru ergonomie, planșa este montată de roboți. Tot ei se ocupă și de montarea parbrizului și lunetei, dar nu înainte de a aplica adezivul special. Tot în acest moment este instalat și acoperișul panoramic. Megane Electric nu are o asemenea opțiune, dar Scenic electric va putea fi echipat cu un plafon panoramic. Sistemul este preluat de la modelele termice.
Pasul următor este asamblarea scaunelor din spate. Până în acest moment, mașina a fost transportată în sensul invers al liniei de fabricație. De acum încolo, ea pornește în sensul normal.
Scaunele față sunt așezate pe poziție, de către oameni, cu ajutorul unui servosistem. Acesta protejează angajații de greutatea pe care acestea ar putea să o exercite asupra corpului. Bineînțeles, îngreunând montarea.
PRIMA PORNIRE A MOTORULUI
Urmează apoi așa numita secție PCM. Adică locul unde mașina este așezată pentru prima oară pe roți și încep primele teste la motor.
Pe 3 bancuri de încercări, angajații uzinei din Douai testează, printre altele, paralelismul roților, reglează farurile, măsoară garda la sol și, nu în ultimul rând, emisiile (unde este cazul). Dar, așa cum vă spuneam mai sus, acest proces va fi eliminat în următorii ani.
Numai după aceea, mașinile ajung pe linia unde sunt făcute toate reglajele (spre exemplu închiderea portierelor etc.) și sunt strânse toate șuruburile la valoarea finală.
Apoi, fiecare mașină produsă aici se "bronzează" în tunelul de lumină. Aici, 15 oameni vigilenți inspectează mașina, pentru posibile neconformități. Lumina ajută ca orice defect să fie sub lupă.
Dacă nu există niciunul, mașina iese pentru prima dată la plimbare. Este un tur de testare pe pista de încercări a uzinei. În timpul testului dinamic, inginerii monitorizează accelerația, frânarea, dar și modul în care se comportă suspensia pe denivelări.
După ce s-a "bronzat" în tunelul de lumină și s-a „murdărit” în timpul testului dinamic, mașina intră înapoi în fabrică pentru un test de apă sub presiune. Pentru a verifica etanșeitatea chederelor și a tot ce înseamnă habitaclu. După acest duș, mașina iese din faza de montare.
În tot departamentul de asamblare lucrează 20 de roboți. Majoritatea operațiunilor sunt efectuate de operatori, astfel că oamenii joacă, încă, un rol foarte important în fabricarea unei mașini la uzina Renault din Douai.
Cei din secția de Montare/Asamblare lucrează în 2 schimburi și, ca timp de muncă, au la dispoziție câte 270 de minute pentru Espace și câte 220 de minute pentru Megane. De ce mai puțin? Pentru că asamblarea unei mașini electrice durează mai puțin, comparativ cu una termică. Pentru început, nu ai un motor cu foarte multe anexe. Iarăși un avantaj în fața mașinilor convenționale.
LUCIANO BIONDO: "ÎN NORDUL FRANȚEI VOR EXISTA DOUĂ MEGA UZINE DE BATERII"
Revenind la subiectul giga uzinelor de baterii, potrivit aceluiași Luciano Biondo, vor exista două mega uzine de baterii în nordul Franței.
"Una va fi construită împreună cu start-up-ul francez Verkor, iar cea de-a doua este un parteneriat cu AESC Envision," a declarat Biondo.
În ceea ce privește Verkor, compania a anunțat în octombrie 2022 că a strâns deja 250 de milioane de euro pentru a finanța construcția acestei mega uzine de baterii.
Întrebat dacă nu crede că implementarea forțată a electrificării dăunează industriei și economiei, directorul Renault ElectriCity a spus că "Dacă vrei ca tehnologia să evolueze, trebuie să ai asemenea strategii." Motivele sunt destul de simple, în opinia lui: protejarea mediului înconjurător (mai exact, schimbările climatice) și sănătatea oamenilor.
"Nu am văzut niciodată ca oamenii să aibă atâtea probleme de sănătate, în special cu respirația. Deci trebuie să facem ceva în acest sens," este de părere Biondo.
A fost atins și subiectul "luptei" dintre Europa și China, în ceea ce privește mașinile cu zero emisii. Luciano Biondo este sigur că Bătrânul Continent poate concura cu țara asiatică din acest punct de vedere.
"Cu un ecosistem creat între producătorii de automobile, Europa și autoritățile fiecărei țări, putem concura cu China. Aș vrea să vă amintesc unde a fost descoperit automobilul: în Europa. Multe dintre tehnologii vin din Europa. Doar că nu trebuie să pierdem timpul cu deliberări stupide și să trecem la treabă", ne-a declarat Biondo, la finalul vizitei noastre.
"Secția de montare are peste 75.000 de metri pătrați. Aici lucrează 1.100 de oameni pe 500 de posturi. Integrează 1.2 kilometri de linie de fabricație, iar aici sunt produse 500 de vehicule în fiecare zi." ... 500 ?!